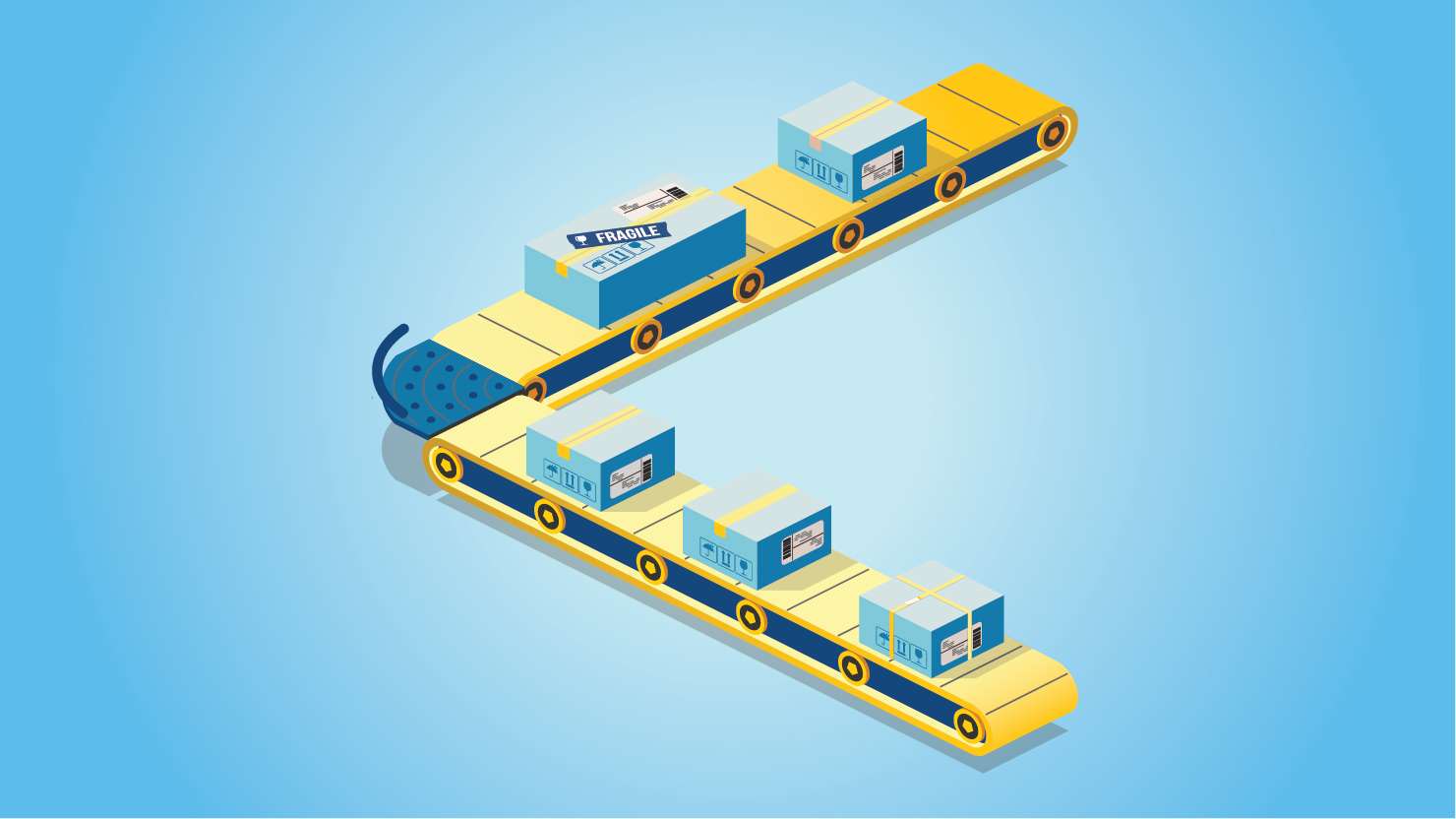
A Conversation With Supply Chain Executives at Lehigh Valley Health Network
April 1, 2019
To lead the transformation of supply chains into the next decade, professionals must identify the opportunities and challenges facing their supply chain processes and consider the resulting impact on the organization, its products and services, and its interactions with suppliers, customers and partners. Drexel LeBow interviews supply chain executives to learn about their roles, their current initiatives and practices, and the future direction of their organizations. This conversation is with Executives Bill Matthews, Vice President of Supply Chain and Allison Hontz, Director, Network Inventory and Logistics at Lehigh Valley Health Network
Q. Traditionally people think supply chain management (SCM) matters only to manufacturing firms and may not realize the importance of SCM to a service organization like Lehigh Valley Health Network. Can you explain the roles that your team plays in ensuring delivery of high-quality health care service to patients in an efficient way?
Simply put, our patients could not be serviced if SCM was not doing their job. SCM provides the physical product to every clinical area for patient care. We also service non-clinical areas by providing items such as tissue boxes to registration desks for guest use. Groups like linen, couriers, printing, copying and mail also support the clinical staff by ensuring they have the products and information (for example, test results or procedure footage moved through the network by couriers) that they need.
SCM departments like analytics and contracting ensure that the SCM division drives quality and value for the organization. These specialty areas assist in progressive supplier management, price discrepancies, equipment purchases (for example, MRIs and IV pumps) and product standardization throughout the network.
All of these functions are critical to the success of our organization.
Q. What is the organizational structure of your group?
SCM is a corporate group, meaning divisions throughout the network report to our vice president. Each northern site (i.e., Schuylkill, Pocono, and Hazleton) has a Director of Materials Management to oversee the site.
For the southern sites (i.e., Cedar Crest, Muhlenberg, 17th Street, Tilghman Street, and Mack), there are two directors: a director of supply chain analytics & purchasing (which oversees SCM analytics and purchasing), and a director of network inventory & logistics (which oversees supply management, inventory management, supply distribution services, linen, couriers, print shop, and mail).
Q. What are the main challenges in managing the supply chain of Lehigh Valley Health Network?
Like many other industries, our SCM division faces two primary challenges: a lack of understanding about supply chain (among our customers and some senior management) and a clash of generations in the workforce.
The most successful Fortune 500 companies are those who really understand the power of supply chain management and leverage it. In healthcare, the focus is patient care. Often the c-suite personnel are clinical and lack experience and exposure to supply chain, unsure of how to leverage supply chain for the benefit of the organization. Further, many are challenged to see value as a comprehensive concept and stick to lowest-price negotiations. This can be very difficult to overcome, and so SCM spends a lot of time educating and emphasizing the value we bring to the organization.
Another asset which provides challenges is our workforce. We have a large contingent of home-grown employees who have only worked for LVHN, and have no advanced degrees, working alongside 30-something MBAs. It can be challenging to engage such a broad audience and keep them motivating each other instead of discouraging each other.
Q. Lehigh Valley Health Network has invested in projects on lean systems in order to minimize waste. Could you share with us some examples of process improvement that resulted from those projects?
One of SCM’s most successful lean projects was on the physical layout of nursing unit product storage (i.e. clean utility). Our nursing units had supply rooms/large closets with fixed cabinets and shelves. Through a lean initiative, waste was identified (such as time spent for SCM and clinical staff to open and close cabinets, reach into low shelves, etc.) and a louvered panel system with hanging bins (plastic or wire) were recommended. We have successfully implemented these systems throughout our sites. This storage system allows for maximum flexibility, ease of use for the clinical staff, ease of delivery for the SCM staff and increased clinical satisfaction overall.
Q. When it comes to making critical purchasing decisions, the purchasing team and physicians may have different opinions. What are the main factors to consider and steps to take before a final decision is made?
It really comes back to value analysis, and the importance that it plays in health care. Purchasing decisions cannot be myopic; they need to take all factors into account. In healthcare, you sometimes run into emotion-based decisions on products. For example, a surgeon may have been taught with a certain line of implants, and he/she is most comfortable with that line. How can you convince someone to consider something they don’t have an attachment to?
SCM works daily on alignment with the clinical staff, teaching them about value in business relationships/partnerships, alliances, commitments, etc.. Every big decision takes time, effort and education for all parties involved. In some cases, what seems like an straightforward comparison of products to SCM really isn’t, and the physicians can teach SCM about it. In the end, it is about forging relationships based on respect with your internal customers and getting a seat at the table.
> Learn more about Drexel LeBow’s MS in Supply Chain Management and Logistics program.